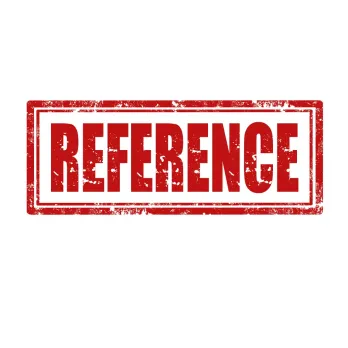
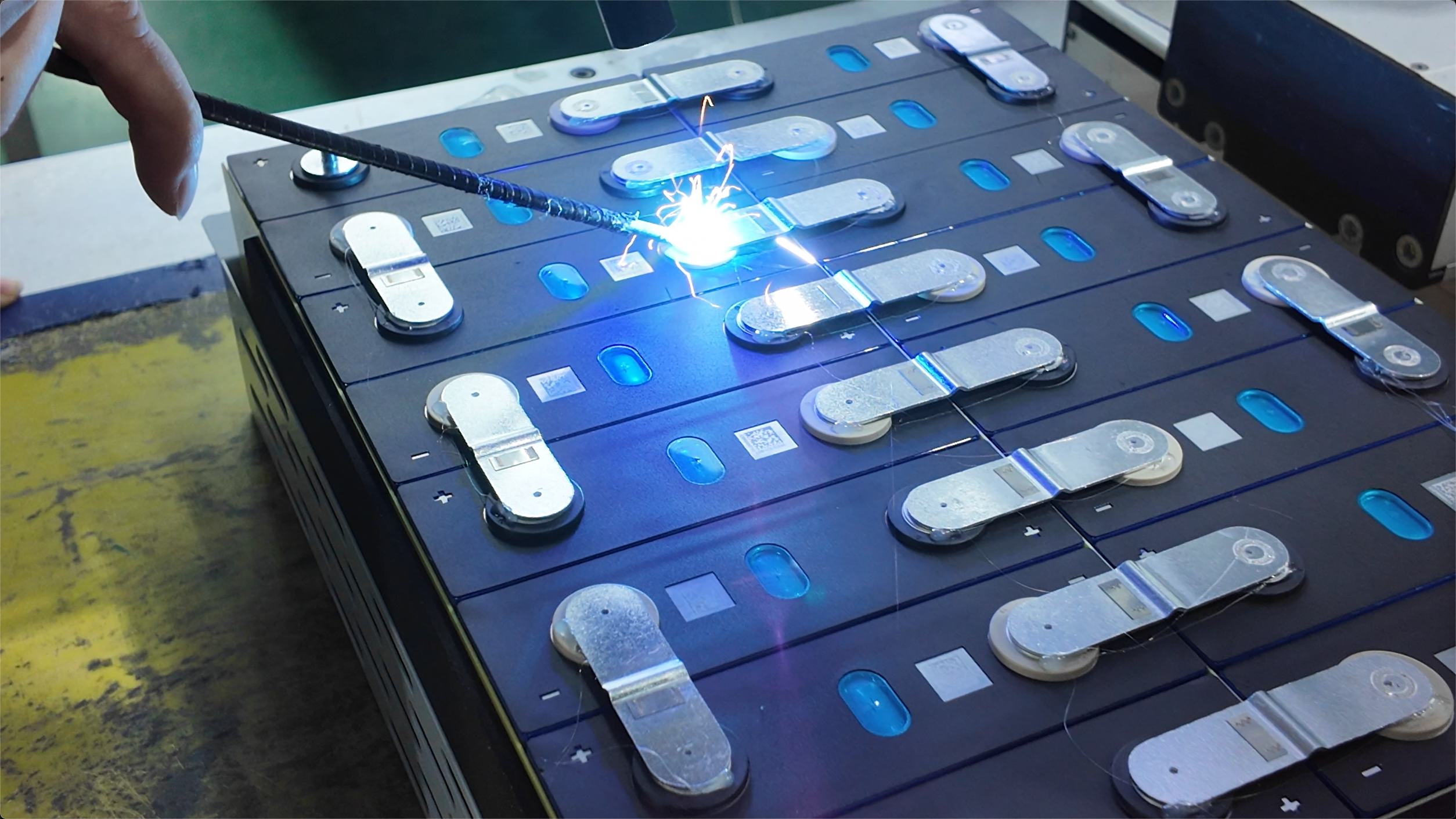
Understanding the Manufacturing Process of Residential Lithium Batteries
As the world transitions to cleaner energy solutions, residential lithium batteries have become an essential component in modern households. They not only store energy from solar systems but also provide backup during outages and help reduce reliance on the grid. Behind each efficient and reliable lithium battery lies a sophisticated manufacturing process that ensures safety, performance, and longevity.
1. Raw Material Selection and Preparation
The manufacturing journey begins with sourcing high-quality raw materials, including:
- Lithium compounds (such as lithium iron phosphate or NMC)
- Graphite for the anode
- Electrolyte solutions
- Aluminum and copper foils
These materials are rigorously tested to meet purity and performance standards.
2. Electrode Manufacturing
The next step is the fabrication of electrodes:
- Mixing: Active materials, binders, and solvents are blended to form a slurry.
- Coating: This slurry is coated onto aluminum foil (for cathodes) or copper foil (for anodes).
- Drying & Rolling: The coated foil is dried and compressed to achieve uniform thickness and density.
3. Cell Assembly
Once electrodes are prepared, the battery cells are assembled in cleanroom environments to prevent contamination:
- Cutting & Stacking: Electrodes and separators are cut and stacked (or wound, for cylindrical cells).
- Welding: Tabs are welded to connect the cell's internal components.
- Electrolyte Filling: The electrolyte is injected under controlled conditions.
- Sealing: The cells are sealed in aluminum-laminated pouches or metal cans.
4. Formation & Aging
This crucial step activates the cell:
- Initial Charging (Formation): The cell is charged and discharged several times to stabilize internal chemistry.
- Aging: The battery is stored for days to monitor self-discharge and identify early defects.
5. Battery Pack Assembly
Individual cells are combined into modules or packs:
- BMS Integration: Battery Management Systems (BMS) are added to monitor voltage, temperature, and current.
- Mechanical Assembly: The cells are secured in housings with insulation and cooling mechanisms.
- Wiring & Protection: Electrical connections and safety circuits are installed.
6. Testing and Quality Control
Every battery pack undergoes strict testing before shipping:
- Capacity & Voltage Checks
- Thermal and Safety Tests
- Cycle Life Simulation
- Compliance Certifications (e.g., UN38.3, CE, IEC)
7. Packaging and Logistics
Finished batteries are carefully packaged to prevent damage during transport and labeled according to international shipping standards for lithium-ion products.